Case: Motor bearing failures with Frequency inverters
Case: The motors from approx 22kw - 250kw and are double star-wound to facilitate a wide speed range. The motors and frequency inverters are matched. The bearings are not showing the usual ESD damage indications but we are experiencing short life (less than 8000 hours in some cases). The bearings on some units are insulated (80kw plus). Is it the bearings that re undersized or if there may be another issue?
Bearings may fail for many reasons, we suggest using the resources of the bearing manufacturer to tell you why the bearings are not providing expected normal life. Once they tell you the cause of the bearing failure, then you can use their corrective action plan.
Motors travel from the factory to destination several hundred to several thousands of miles. The bearings are being damaged by the vibration of the transport means. Some users will automatically replace the bearing and pack them with suitable grease for the intended application.
The grease installed at the motor manufacturer plant may not be suitable for the application at the users location.
Temperatures of the NDE and DE bearing could be significantly different requiring two different viscosities of grease for the actual operating temperatures. The viscosity of the selected grease must match the bearing clearance dimension at the bearing running temperature otherwise the bearing will fail due to poor lubrication.
Once you have a frequency inverter rated motor, If this is a an application where the shaft is ungrounded, i.e. a blower, you may need the solutions mentioned above, to isolate the bearings from bearing current flow, or giving the current a path to ground, i.e. grounding rings etc. As well if the distance of the output inverter cables to the motor is in excess of 100 meters, the terminal voltage may increase due to the Fast rise time of the frequency inverter output, cable capacitance and propagation and motor damage can result. Proper frequency inverter output cable can mitigate this issue. As you've also looked at the bearing grease, I'd also insure the mechanical system is not causing vibration or contributing to mechanical resonance. Hang in there as this issues that can cause these problems can be fairly difficult to find.
There have been occasions where of a small amount of electrical discharge through the bearing lubricant can cause additional heating and subsequent lubricant breakdown. This then precipitates a bearing failure mode that often will wipe out the evidence of the arching / pitting inside the bearing race that might point to the initial cause.
The only way to determine if this is actually happening is to analyze the motor shaft bearings BEFORE they fail. It is mentioned that some bearings are failing in less than 8000 hours of run time. I suggest proactively dismantling, cutting open and examining the motor bearings at intervals of 6,000 hours, and 10,000 hours and perhaps 15,000 hours. As was suggested, have the motor and bearing manufacturer participate in this process as well. If possible, try to select a motor location where the failures have been most frequent. Note: Convincing production management to allow this may be more difficult than actually turning the wrenches.
If this proves to be an electrical discharge issue, the remedies vary in cost and complexity. Involving the machinery and motor manufacturers may bring additional resources that can expedite a resolution.
Bearings may fail for many reasons, we suggest using the resources of the bearing manufacturer to tell you why the bearings are not providing expected normal life. Once they tell you the cause of the bearing failure, then you can use their corrective action plan.
Motors travel from the factory to destination several hundred to several thousands of miles. The bearings are being damaged by the vibration of the transport means. Some users will automatically replace the bearing and pack them with suitable grease for the intended application.
The grease installed at the motor manufacturer plant may not be suitable for the application at the users location.
Temperatures of the NDE and DE bearing could be significantly different requiring two different viscosities of grease for the actual operating temperatures. The viscosity of the selected grease must match the bearing clearance dimension at the bearing running temperature otherwise the bearing will fail due to poor lubrication.
Once you have a frequency inverter rated motor, If this is a an application where the shaft is ungrounded, i.e. a blower, you may need the solutions mentioned above, to isolate the bearings from bearing current flow, or giving the current a path to ground, i.e. grounding rings etc. As well if the distance of the output inverter cables to the motor is in excess of 100 meters, the terminal voltage may increase due to the Fast rise time of the frequency inverter output, cable capacitance and propagation and motor damage can result. Proper frequency inverter output cable can mitigate this issue. As you've also looked at the bearing grease, I'd also insure the mechanical system is not causing vibration or contributing to mechanical resonance. Hang in there as this issues that can cause these problems can be fairly difficult to find.
There have been occasions where of a small amount of electrical discharge through the bearing lubricant can cause additional heating and subsequent lubricant breakdown. This then precipitates a bearing failure mode that often will wipe out the evidence of the arching / pitting inside the bearing race that might point to the initial cause.
The only way to determine if this is actually happening is to analyze the motor shaft bearings BEFORE they fail. It is mentioned that some bearings are failing in less than 8000 hours of run time. I suggest proactively dismantling, cutting open and examining the motor bearings at intervals of 6,000 hours, and 10,000 hours and perhaps 15,000 hours. As was suggested, have the motor and bearing manufacturer participate in this process as well. If possible, try to select a motor location where the failures have been most frequent. Note: Convincing production management to allow this may be more difficult than actually turning the wrenches.
If this proves to be an electrical discharge issue, the remedies vary in cost and complexity. Involving the machinery and motor manufacturers may bring additional resources that can expedite a resolution.
You may also like:
Surge and hipot testing can be potentially destructive. But, so can a Megger test on a motor which is in very poor condition. When testing a motor, tests are performed starting with the low voltage tests and ...
we must not get confused and think very simply that soft-start and variable frequency drive have the same role. AC drives are more expensive and soft starters are not able to regulate frequency. There are many ...
A)- Rating equal 150% of the primary current (under no circumstances to be more than 300% - this is exceptional if the adopted secondary fuse rating at LV not exceeding 125% of the secondary full load ...
Radiated noise from an AC drive cable is a source of interference with adjacent systems that is often easier to identify and rectify than common mode noise. In the latter, high levels of noise across a broad ...
On the delta side you use the term BEF but I would still simply call it REF - the "B" doesn't necessarily indicate a differential type protection as there are other instances where unrestricted earth fault ...
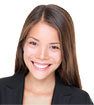
Hot Tags
Featured
Frequency directly represents no of rotation of rotor for that machine,
the higher the frequency the more the rotation of the rotor, i.e. the
rpm of the motor there by result ...
Due to power electronics technology and microelectronics technology rapid development, variable frequency drive reforms and upgrades speed also is faster, introduce new products, ...
Since the 21st century, China variable frequency drive industry is highly fission. Many foreign brands begin to set up factories in China, the implementation of the localization ...
My personal preference is for an AC line reactor simply because it does a better job of protecting the variable frequency drive from the line and the line from the drive. I've ...
As nowadays there is a trend in green energy production and energy efficiency, what solutions/applications would you recommend in reduction consumed energy of a motor driven by ...
What's New
What are the effects for a 50Hz motor running on 60Hz?
Variable Frequency Drive versus Soft Starter in Harmonics
Considerations in choosing large Variable Frequency Drive
Common Mode Noise Impact in AC drive Applications
AC drives in pumps for energy saving
HMI and SCADA system
Something need to be considered in buying AC drives
ABB sine wave filter
Variable Frequency Drive versus Soft Starter in Harmonics
Considerations in choosing large Variable Frequency Drive
Common Mode Noise Impact in AC drive Applications
AC drives in pumps for energy saving
HMI and SCADA system
Something need to be considered in buying AC drives
ABB sine wave filter