Home » Blog » Variable frequency drive » Energy savings with variable frequency drives
Energy savings with variable frequency drives
As nowadays there is a trend in green energy production and energy efficiency, what solutions/applications would you recommend in reduction consumed energy of a motor driven by variable frequency drive. Almost all respectful VFD manufacturers, has a energy saving calculator mainly for ventilation and pump applications (variable torque).
A VFD is already energy efficient, as opposed to changing from DC Drives to VFD. However I have found one key element to energy conservation - operational speed and installed speed. A 4 pole motor running at 600 to 900 rpm, changed to a 6 pole motor will make considerable savings. A motor running slowly does not produce the kw's for the job, a motor running closer to rated speed does. The key lies in the application / production speed, and the installed motor speed.
Energy saving using VFDs is always vary application to application. Following points you need to consider before using VFDs for energy saving.
1. How much process flow and pressure requirement through AC motors
2. Existing control methodology like control valve in pumps, Damper or guide vane for Fans & Blowers etc. and position of the valve or dampers
3. If you have process flow and pressure data and pump or fan design data, you can calculate energy saving using affinity law
4. Loading and Unloading cycle for compressor application. If the unloading time is higher for compressor application, you will get better energy saving
5. Using affinity law, you can calculate the energy saving with consideration of VFD losses. With this you can calculate the Pay back of VFDs.
The power factor standard was not set up correctly to begin with. The standard the way it has currently been set up, rewards consumers for increasing their efficiency of energy consumption and penalizes consumers for decreasing their efficiency of energy production. What is wrong with this picture? Shouldn't an energy use efficiency standard reward consumers for conservation and shower the consumer with accolades for participating in production to meet our growing demands? (the exact opposite of what we are seeing the utility companies advocate today) Something is rotten in Denmark. A consumption vs production energy standard would be a much better standard than an increase in efficiency of use vs a decrease in efficiency of energy use standard. Who initiated this standard anyways? If I were a customer paying demand charge penalties for being more of a producer than a consumer, I would not stand for it!
Simply put a VFD can save energy COMPARED to OTHER means of VARYING flow and/or pressure in centrifugal machines, like pumps and fans. If you are not VARYING the speed, you will not save energy, regardless of whether is is full speed or not. There are more cost effective means of permanently CHANGING the output if it will run continuously at that output. But if VARYING the speed is a part of your process (the work that the machine does), then compared to OTHER methods of accomplishing that, a VFD will save significant energy. This is a very commonly misunderstood and overstated part of the picture.
The other time I have seen VFDs save energy in non-centrifugal machines is when mechanical vari-drives are used, such as variable pulley systems, hydraulic drives, particle clutches etc., but only IF it is only speed control you are after (as opposed to torque multiplication when using a vari-drive for instance). The losses in a VFD are slightly lower than the losses in most other non-electronic speed control methods.
A VFD is already energy efficient, as opposed to changing from DC Drives to VFD. However I have found one key element to energy conservation - operational speed and installed speed. A 4 pole motor running at 600 to 900 rpm, changed to a 6 pole motor will make considerable savings. A motor running slowly does not produce the kw's for the job, a motor running closer to rated speed does. The key lies in the application / production speed, and the installed motor speed.
Energy saving using VFDs is always vary application to application. Following points you need to consider before using VFDs for energy saving.
1. How much process flow and pressure requirement through AC motors
2. Existing control methodology like control valve in pumps, Damper or guide vane for Fans & Blowers etc. and position of the valve or dampers
3. If you have process flow and pressure data and pump or fan design data, you can calculate energy saving using affinity law
4. Loading and Unloading cycle for compressor application. If the unloading time is higher for compressor application, you will get better energy saving
5. Using affinity law, you can calculate the energy saving with consideration of VFD losses. With this you can calculate the Pay back of VFDs.
The power factor standard was not set up correctly to begin with. The standard the way it has currently been set up, rewards consumers for increasing their efficiency of energy consumption and penalizes consumers for decreasing their efficiency of energy production. What is wrong with this picture? Shouldn't an energy use efficiency standard reward consumers for conservation and shower the consumer with accolades for participating in production to meet our growing demands? (the exact opposite of what we are seeing the utility companies advocate today) Something is rotten in Denmark. A consumption vs production energy standard would be a much better standard than an increase in efficiency of use vs a decrease in efficiency of energy use standard. Who initiated this standard anyways? If I were a customer paying demand charge penalties for being more of a producer than a consumer, I would not stand for it!
Simply put a VFD can save energy COMPARED to OTHER means of VARYING flow and/or pressure in centrifugal machines, like pumps and fans. If you are not VARYING the speed, you will not save energy, regardless of whether is is full speed or not. There are more cost effective means of permanently CHANGING the output if it will run continuously at that output. But if VARYING the speed is a part of your process (the work that the machine does), then compared to OTHER methods of accomplishing that, a VFD will save significant energy. This is a very commonly misunderstood and overstated part of the picture.
The other time I have seen VFDs save energy in non-centrifugal machines is when mechanical vari-drives are used, such as variable pulley systems, hydraulic drives, particle clutches etc., but only IF it is only speed control you are after (as opposed to torque multiplication when using a vari-drive for instance). The losses in a VFD are slightly lower than the losses in most other non-electronic speed control methods.
You may also like:
AC reactors reduce harmonics, mitigates transient conditions and helps to maintain proper phase to phase voltages. DC reactors will also mitigate harmonics however it will provide more harmonic attenuation ...
HMI stands for Human Machine Interface and HMI is a term and not an application.
HMI is the communication/interaction layer between the user and the process.
In the process industry the "Human" is the ...
I have been in the electric motor repair industry all my working life, (50 years) and I have watched this industry progress. During my apprenticeship in the UK we were taught all about the damages that can be ...
No matter what level of voltage you are dealing with, the ground wall insulation will be heavier than the conductor insulation. Potential to the ground wall is line voltage. Turn to turn voltage, especially in ...
Bridges are very common in Hi-Reli applications such as aircraft and almost necessary for inverters and variable frequency drives. I'm curious to hear which type of industry exhibited these "recent rumblings" ...
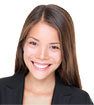
Hot Tags
Featured
Frequency directly represents no of rotation of rotor for that machine,
the higher the frequency the more the rotation of the rotor, i.e. the
rpm of the motor there by result ...
Due to power electronics technology and microelectronics technology rapid development, variable frequency drive reforms and upgrades speed also is faster, introduce new products, ...
Since the 21st century, China variable frequency drive industry is highly fission. Many foreign brands begin to set up factories in China, the implementation of the localization ...
My personal preference is for an AC line reactor simply because it does a better job of protecting the variable frequency drive from the line and the line from the drive. I've ...
As nowadays there is a trend in green energy production and energy efficiency, what solutions/applications would you recommend in reduction consumed energy of a motor driven by ...
What's New
What are the effects for a 50Hz motor running on 60Hz?
Variable Frequency Drive versus Soft Starter in Harmonics
Considerations in choosing large Variable Frequency Drive
Common Mode Noise Impact in AC drive Applications
AC drives in pumps for energy saving
HMI and SCADA system
Something need to be considered in buying AC drives
ABB sine wave filter
Variable Frequency Drive versus Soft Starter in Harmonics
Considerations in choosing large Variable Frequency Drive
Common Mode Noise Impact in AC drive Applications
AC drives in pumps for energy saving
HMI and SCADA system
Something need to be considered in buying AC drives
ABB sine wave filter