Home » Blog » Energy saving » What causes Power Supplies Failed?
What causes Power Supplies Failed?
A few years ago I wrote an article listing the things that can often fail in power supplies. Despite its simplicity, the article was the most downloaded on the website for a long time. Maybe that tells us something about the state of reliability as cost constantly gets battled down.
When a power supply fails, the semiconductors almost ALWAYS blow up. But that doesn't always mean that the semiconductors are to blame. They are just the parts that give way first when things go wrong.
For example, saturating magnetics will put too much current through the FET and eventually destroy it. But the magnetics are then to blame. It takes a lot to burn the magnetics, and the FET gives out before then.
Many times I have seen control chips put out bad signals, and the victim is the power FET, but the FET is not the cause.
I see this thermal issue a lot. One company I worked with was using a SOT-23 FET and I measured the temperature with an IR probe at around 130 degrees, with room temp operation. It clearly wasn't going to survive high ambient.
The company was surprised since they had measured the temperature rise much lower than this. They had used a hefty thermocouple glued to the part, which provide far more conduction cooling than existed on the board.
The low on-resistance parts in a tiny package look great until you realize the surface area to cool them is the same as it ever was. The constant for thermal impedance with convection cooling hasn't changed with the introduction of new packaging.
In this case, the semiconductor is overstressed, but the mechanical design is actually to blame. I probably should have worded the survey question better.
Semiconductors often suffer consequential damage. But since you obviously meant power supplies "in toto" that includes all those that came with gear in our possession where things eventually got *PHUT*. Where some designer thought that an 8A Schottky is going to be ok because most PCs won't run full bore all the time. Then you do a long SPICE sim and ... poof. Or the little modulator that let's us watch movies on the deck. A DPAK in there was way underserved for heat sinking and it went kaputt. They had set aside a whopping 1 (one) square inch of copper that was 0.25oz at best, to vent almost 2W inside a plastic enclosure. After replacing and giving it a nice heat sink it never happened again.
The other notorious design issue are gate resistors. I never use them unless I really, really have no other choice. The usual reasons I hear are "Otherwise we don't pass radiated EMC" or "Else we get body diode shoot-through". Then you see the efficiency of the converter drop a wee bit. Pretty much all this additional loss has to be stomached by the FETs or IGBTs. Temperatures rise, reliability goes down.
It always puzzles me why folks use muscular 1 ohm gate drivers and then place 22 ohms in series with the gates.
Of course this can also not be chalked up to the semiconductors but that's the ones that will go kaputt. In the end nearly everything is collateral damage. Like capacitors, Yeah, they fail. But mostly that is because someone thought it's ok to put 3A ripple current on a caps that is barely rated at that, or maybe because someone placed an electrolytic cap next to a heatsink that gets hot. Those not so optimal design decisions almost date back to Methusaleh. For example, the electrolytic in our 1961 Hammond organ lives right next to the hottest part in the whole chassis, the big rectifier tube.
We might someday start seeing a new category of failures once digital makes more serious inroads into power supplies. When people start using DSP in large BGA packages. That combined with a mechanically stressed and thermally exercised environment can result in issues.
When a power supply fails, the semiconductors almost ALWAYS blow up. But that doesn't always mean that the semiconductors are to blame. They are just the parts that give way first when things go wrong.
For example, saturating magnetics will put too much current through the FET and eventually destroy it. But the magnetics are then to blame. It takes a lot to burn the magnetics, and the FET gives out before then.
Many times I have seen control chips put out bad signals, and the victim is the power FET, but the FET is not the cause.
I see this thermal issue a lot. One company I worked with was using a SOT-23 FET and I measured the temperature with an IR probe at around 130 degrees, with room temp operation. It clearly wasn't going to survive high ambient.
The company was surprised since they had measured the temperature rise much lower than this. They had used a hefty thermocouple glued to the part, which provide far more conduction cooling than existed on the board.
The low on-resistance parts in a tiny package look great until you realize the surface area to cool them is the same as it ever was. The constant for thermal impedance with convection cooling hasn't changed with the introduction of new packaging.
In this case, the semiconductor is overstressed, but the mechanical design is actually to blame. I probably should have worded the survey question better.
Semiconductors often suffer consequential damage. But since you obviously meant power supplies "in toto" that includes all those that came with gear in our possession where things eventually got *PHUT*. Where some designer thought that an 8A Schottky is going to be ok because most PCs won't run full bore all the time. Then you do a long SPICE sim and ... poof. Or the little modulator that let's us watch movies on the deck. A DPAK in there was way underserved for heat sinking and it went kaputt. They had set aside a whopping 1 (one) square inch of copper that was 0.25oz at best, to vent almost 2W inside a plastic enclosure. After replacing and giving it a nice heat sink it never happened again.
The other notorious design issue are gate resistors. I never use them unless I really, really have no other choice. The usual reasons I hear are "Otherwise we don't pass radiated EMC" or "Else we get body diode shoot-through". Then you see the efficiency of the converter drop a wee bit. Pretty much all this additional loss has to be stomached by the FETs or IGBTs. Temperatures rise, reliability goes down.
It always puzzles me why folks use muscular 1 ohm gate drivers and then place 22 ohms in series with the gates.
Of course this can also not be chalked up to the semiconductors but that's the ones that will go kaputt. In the end nearly everything is collateral damage. Like capacitors, Yeah, they fail. But mostly that is because someone thought it's ok to put 3A ripple current on a caps that is barely rated at that, or maybe because someone placed an electrolytic cap next to a heatsink that gets hot. Those not so optimal design decisions almost date back to Methusaleh. For example, the electrolytic in our 1961 Hammond organ lives right next to the hottest part in the whole chassis, the big rectifier tube.
We might someday start seeing a new category of failures once digital makes more serious inroads into power supplies. When people start using DSP in large BGA packages. That combined with a mechanically stressed and thermally exercised environment can result in issues.
You may also like:
Due to power electronics technology and microelectronics technology rapid development, variable frequency drive reforms and upgrades speed also is faster, introduce new products, improve performance ...
Motor Circuit Analysis (MCA) is a de-energized test method and the test can be initiated from the Motor Control Center (MCC) or directly at the motor. The advantage to testing from the MCC is the entire motor ...
Power factor is actually the factor of generated power utilized in performing useful work.
Ideally it is equal to 1, but practically it is always less than 1 as current always take time to reach at lower ...
The motor I need to stop is a 90W Single Phase Permanent Capacitor Induction motor, run straight from 230V AC mains. I'm not able to use a variable speed drive, separate DC injection braking unit or a DC ...
Variable Frequency Drives (VFD) that do not have either an AC line reactor or a DC bus choke, will typically exhibit a THDi greater than 85% at all loading conditions. The THDi is dependent on the conduction ...
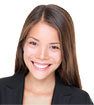
Hot Tags
Featured
Frequency directly represents no of rotation of rotor for that machine,
the higher the frequency the more the rotation of the rotor, i.e. the
rpm of the motor there by result ...
Due to power electronics technology and microelectronics technology rapid development, variable frequency drive reforms and upgrades speed also is faster, introduce new products, ...
Since the 21st century, China variable frequency drive industry is highly fission. Many foreign brands begin to set up factories in China, the implementation of the localization ...
My personal preference is for an AC line reactor simply because it does a better job of protecting the variable frequency drive from the line and the line from the drive. I've ...
As nowadays there is a trend in green energy production and energy efficiency, what solutions/applications would you recommend in reduction consumed energy of a motor driven by ...
What's New
What are the effects for a 50Hz motor running on 60Hz?
Variable Frequency Drive versus Soft Starter in Harmonics
Considerations in choosing large Variable Frequency Drive
Common Mode Noise Impact in AC drive Applications
AC drives in pumps for energy saving
HMI and SCADA system
Something need to be considered in buying AC drives
ABB sine wave filter
Variable Frequency Drive versus Soft Starter in Harmonics
Considerations in choosing large Variable Frequency Drive
Common Mode Noise Impact in AC drive Applications
AC drives in pumps for energy saving
HMI and SCADA system
Something need to be considered in buying AC drives
ABB sine wave filter